Weaving traditional handlooms is now easier, thanks to this serial innovator
With widespread use of devices like these, the dying art of traditional handloom weaving will receive a fillip, and the legacy of weaving communities will continue to flourish, thanks to innovators like Dipak.
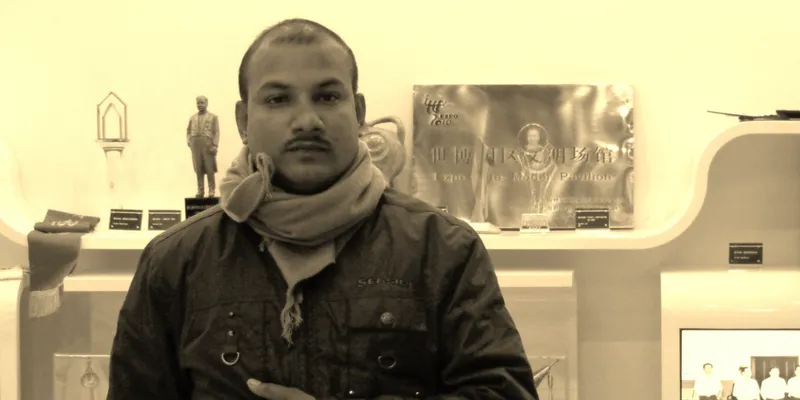
Traditional handlooms are dying. According to this report, the growth in power looms, now supplying more than 70 percent of Indian textiles, has come on the heels of a systematic destruction of the handloom industry.
But there are some like Dipak Bharali, a traditional weaver who soldier on. He weaves on silk which is an intricate art, and requires hours of manual hard work that involves intricate threadwork that is done by tying knots.
Dipak is a muga silk weaver from Assam, who has not cowed down to the dictates of modern weaving. He still follows the traditional path and does not use any modern machinery.
Circumstances however, have compelled him to innovate. To cut down the time taken in weaving and to make the process easier, he invented a device that has made his and the lives of other silk weaver easier. For his invention, he also won the 5th National Grassroots Innovation Awards in 2009.
Carrying forward a tradition
Dipak hails from Assam’s Kamrup district, popularly known as the ‘Manchester of the East’. The economy of his village is primarily dependent on weaving of muga silk using traditional looms.
Dipak’s family has been engaged in production and trading of silk goods for decades. His father was a distributor of silk items. After completing his graduation, and following the death of his parents, he decided to continue the family business.
He started with his first loom in 1998 by weaving plain cloth without any form of design on it. Using the looms himself, he wove the cloth and learnt about various aspects of production. After nine months, he installed his second loom and diversified into producing silk with designs.
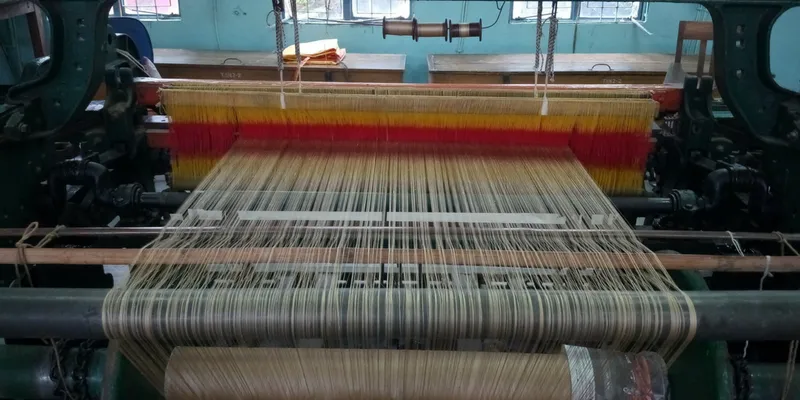
By this time, he was looking to expand by increasing production and adding more looms. He found that this idea was fraught with many challenge. Hiring skilled workers was expensive, and only people from his community were adept at the art of muga silk weaving.
“An average fabric has 30 rows of lines and 14 designs in a row with each design requiring at least 3 knots. This meant that a total of 1260 knots would require almost 10 hours, assuming the weaver takes 30 seconds to make each knot,” he explains.
Also production of designer handwoven silk require handling of five or more threads simultaneously which only a few skilled weavers possessed.
The hard work involved is deterring many from joining the profession, and most third and fourth-generation weavers are leaving the trade. Another deterrent is the low pay.
To increase production speed, automate and cut down the repetitive process in routine tasks, Dipak decided to create a dedicated fixture style attachment that could be attached to the standard loom.
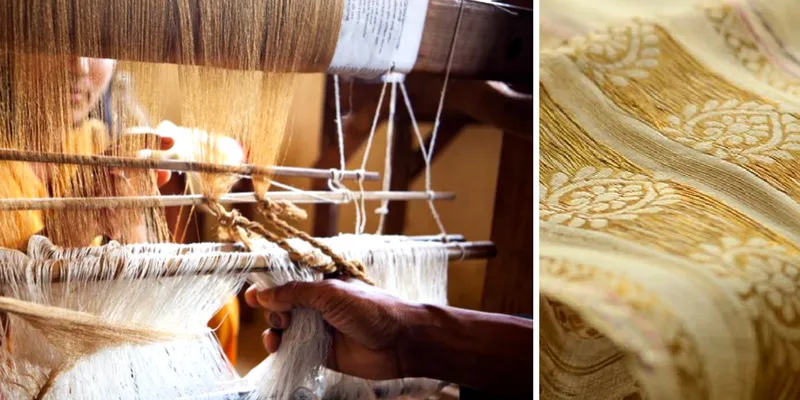
The most common weaving machine available and in use today is the Jacquard loom, a machine invented by Joseph-Marie Jacquard. Dipak’s device does not eliminate the Jacquard loom but enhances its production capacity and reduces the time taken to weave by one-third.
Making the weaving process easier
The device consists of three components - a base frame which acts as a shaft holder, the magnet bearing shaft and the specially designed bobbin. The attachment facilitates the loom to not only automatically select but also lift the threads for design making.
The magnetic shaft is integrated into the base frame.
“In a normal Jacquard loom each thread is connected to a bobbin. Here, the device is placed in such a way that the bobbin’s attached surface faces downwards and each bobbin falls in between two sets of lifted threads,” he explains.
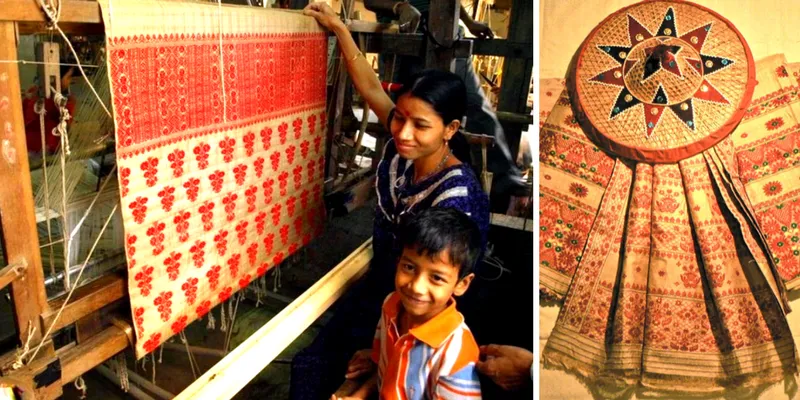
As the magnet fitted shaft moves from one side to the other, it also drags along the bobbins attached to it from one side to other. In the process, the simultaneous crossing of all weft threads for design making takes place.
The device has resulted in an increase in productivity by 60 per cent, ease of use and better fabric quality. Further, this attachment also allows unskilled workers to enter the industry and produce elaborately designed fabrics.
Currently, this device is receiving product development support from IIT Guwahati and financial support by the National Innovation Foundation.
The making of a serial inventor
The seventh child of his parents, Dipak was curious child and had a keen eye for detail, from a young age.
He recalls a particular incident that happened when he was a child. While pulling out an old cycle tyre from a ditch he observed that the inner sides of the tyre were lined with different types of small fish. He was intrigued, and as an experiment dropped another tyre into the ditch and noticed that after few hours this tyre, too, was filled with fish. Since then, this become his unique technique for catching fish.
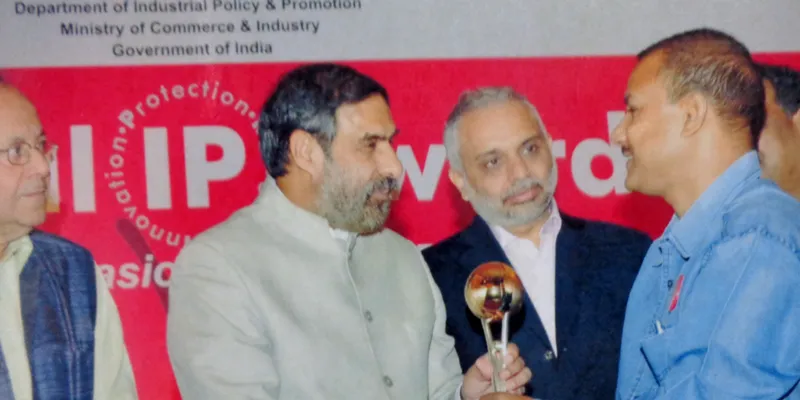
Every available object, even discarded bearings, is utilised by him to invest daily utility objects, including model cars.
Weaving a future of convenience
Dipak has set up the preliminary device in his nineteen looms, now supervised by his younger brother. Since 2013, he has immersed himself completely in refining the model of this invention and make his device accessible across India and neighbouring countries. Currently the device is also available for order and is priced at Rs 7,000. Further the central government has also subsidised his device and is helping him promote the device across different states.
Dipak dreams of making his device available to the power loom sector as well.
“Generally, in power looms the insertion of extra weft (criss-cross threads) is done by using shuttle (a tool designed to neatly store a thread holder). The unused portion is cut abruptly. Such cloth normally looses its demand in the market.”
Supported by his family members in developing new tools and devices for silk production, Dipak today runs 19 looms successfully.