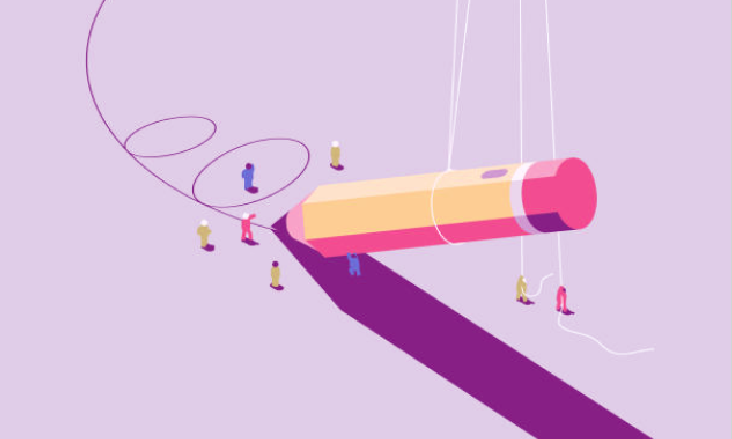
How a manufacturing and supply industry can survive COVID-19?
COVID-19 has really put the business world through a ringer where your resolve, and adaptability is tested. In this article, we take a look at one company and draw parables which can help manufacturing and supply industry survive this brave new world.
When the first case of COVID-19 arrived in January, many were sleeping in the bed of complacency. Believing the disease to either be a hoax or temporary nuisance, they carried on like it was nothing. Now, 5 months later, global economy is in shambles. It now expects to suffer anywhere between $5.8 trillion to $8.8 trillion in losses. From that you can get the picture of what has happened to those “sleeping” enterprises.
But, there were some who didn’t take the complacent route. They had a hint of what COVID-19 could do to their business; of how it can shake their financial foundation. That foresight made them vigilant – leading them to adapt quickly when the pandemic finally went global. Now, they stand as an inspiration of how a manufacturing and supply industry can survive the onslaught of COVID-19.
In this article, we showcase one such company. Navigate its process and see how it operates business during pandemic. In doing so, the parables drawn will help your business perform at a high capacity during this time of pandemic.
Proactively adapting to a restrictive work environment
While talking to RoboticsTomorrow, Universal Robots stressed on how being proactive helps them generate profits even during pandemic. After the first COVID-19 cases in January, they prepared themselves to adapt to a restrictive scenario – having the foresight to assume that the virus might go global. And we all know how true their assumptions were.
Anyway, being a tech-based company, most of the employees who aren’t directly involved with the physical production of the product were told to only work from home.
As for professionals working in physical production, Universal Robots opted to send robots to their homes. Those professionals were then able to setup a mini manufacturing plant in their very own garage. To aid coordination between employees who are involved, Universal Robots implemented their in-house simulation software.
Lesson 1:
Employees who possess the capability to work offsite in your manufacturing company should be allowed to do to work from home. If you are worried about productivity, look for tech-based solutions that will help them coordinate better with your other employees.
Implementing Visionary Dual Sourcing Strategy
When asked how they were able to ensure that the supply chain is not hampered during pandemic, Universal Robot replied that although COVID-19 has severely limited their movement, they already had a dual source supply chain in place.
Dual Sourcing is a supply-chain practice to use two different sources/suppliers for raw materials, services, products or components.
By implementing the dual sourcing strategy, Universal Robots lessened the impact on its supply chain movement when its China and Europe plants started shutting down.
Lesson 2:
You should implement a Visionary Dual source strategy. A visionary dual source strategy is where you dynamically choose multiple suppliers on the fly to deal with any sudden adversities faced by your supply chain. More often than not, it’s an instinctive decision that you can only take after being knowledgeable and informed about the current business scenario.
Minimizing the risk while maintaining the production line
Universal Robots has taken the following measures to minimize the risk of infection among its employees:
- 2 meter distancing: As per WHO recommendation, the company has made social distancing a norm, with each employee given workspace 2 meter apart from his/her colleague.
- Hand sanitation stations: The Company has installed multiple hand-sanitation stations to minimize the chance of infection.
- Gloves availability: It has made mandatory for the employees to wear rubber gloves at all times.
To maintain the production line, the Universal Robots has implemented two-shift operation to spread out its workforce. Doing so has bestowed it with two benefits:
- The production facilities aren’t overcrowded because only half of the employees are working.
- Spreading out the production time means more time is spent on production to maintain a steady product supply.
Lesson 3:
Spread out your production time and ensure that your employees stay safe. Dual-shift helps your manufacturing unit keep up with the demands, and implementing COVID-19 protection measures will ensure that your employees are protected from any unintended exposure.
Redundant Warehousing to circumvent mobility issues
The speed at which COVID-19 pandemic has spread has put the whole world at a grinding standstill. To keep moving, the robot manufacturing company implemented redundant warehousing. By keeping multiple warehouses, the company is able to deliver products from one warehouse if there is a COVID-19 outbreak in another. This method ensures timely delivery of end-products to the customers.
Lesson 4:
Even if you are a budding manufacturing company, you need to find a way to acquire multiple warehouses. Rent them if you can. In times when there is a negative impact on mobility, having warehouses in proximity to recipient locations can and will help you deliver the end products on time.
Final Lesson: Trust and communication
All the investment in redundant warehouses and automation would be in vain if you don’t learn the cores of the first three lessons: they are trust and communication.
Adapting to a restrictive work environment isn’t possible without your trust in your employees. Likewise, maintaining the production line and spreading out the production time isn’t possible without
your employees’ trust in you. Finally, implementing dual strategy isn’t possible without keeping close contact with multiple suppliers.
- If you don’t trust your employees to do their job, you will always second guess the quality of their work. Your distrust would be a deterrent to their productivity that will cause lack of coordination between your employees, hampering the production.
- If your employees don’t put their trust in you, they would second guess your willingness to pay their dues on time. This puts them in a half-hearted mood to commit to their prescribed tasks. The result is a slow production process -- putting a negative impact on your timeline.
- If you don’t keep close contact with your suppliers than the double-sourcing strategy won’t work. The time of pandemic is a crucial one and a single miscommunication between you and your suppliers can lead to disastrous consequences.
Conclusion
COVID-19 has created a new normal for entrepreneurs. To adapt to this brave new normal, you have to be more passionate, more trusting and should possess more foresight to make decisions on the fly. If you succeed in imbibing all the right lessons and implement them with thoughtful pragmatism, there is a chance for your business to grow stronger when the pandemic cloud finally lifts.